Toyota Sienna Service Manual: Adjustment
1. VEHICLE PREPARATION FOR HEADLIGHT AIMING
ADJUSTMENT
- Prepare the vehicle:
- Ensure there is no damage or deformation to the
body around the headlights.
- Fill the fuel tank.
- Make sure that the oil is filled to the specified
level.
- Make sure that the coolant is filled to the
specified level.
- Inflate the tires to the appropriate pressure.
- Place the spare tire, tools, and jack in their
original positions.
- Unload the trunk.
- Sit a person of average weight (68 kg, 150 lb) in
the driver's seat.
2. PREPARATION FOR HEADLIGHT AIMING (Using a
tester)
- Prepare the vehicle for headlight aim check.
- Adjust in accordance with headlight tester
instructions.
3. PREPARATION FOR HEADLIGHT AIMING (Using a
screen)
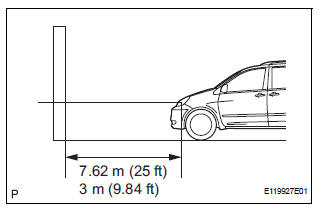
- Prepare the vehicle according to the following
conditions:
- Place the vehicle in a location that is dark
enough to clearly observe the cutoff line. The
cutoff line is a distinct line, below which light from
the headlights can be observed and above which
it cannot.
- Place the vehicle at a 90 angle to the wall.
- Create a 7.62 m (25 ft) distance between the
vehicle (headlight bulb center) and the wall.
- Place the vehicle on a level surface.
- Bounce the vehicle up and down to settle the
suspension.
NOTICE:
A distance of 7.62 m (25 ft) between the
vehicle (headlight bulb center) and the wall is
necessary for proper aim adjustment. If
unavailable, secure a distance of exactly 3 m
(9.84 ft) for check and adjustment. (The target
zone will change with the distance so follow
the instructions in the illustration.)
- Prepare a piece of thick white paper (approximately
2 m (6.6 ft) (height) x 4 m (13.1 ft) (width)) to use as
a screen.
- Draw a vertical line down the center of screen (V
line).
- Set the screen as shown in the illustration.

HINT:
- Stand the screen perpendicular to the ground.
- Align the V line on the screen with the center of
the vehicle.
- Draw base lines (H line, V LH, V RH lines) on the
screen as shown in the illustration.
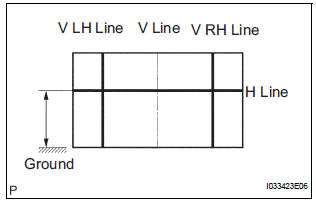
HINT:
- The base lines differ for "low-beam inspection"
and "high-beam inspection."
- Mark the headlight bulb center marks on the
screen. If the center mark cannot be observed
on the headlight, use the center of the headlight
bulb or the manufacturer's name marked on the
headlight as the center mark.
- H Line (Headlight height):
Draw a horizontal line across the screen so that
it passes through the center marks. The H line
should be at the same height as the headlight
bulb center marks of the low-beam headlights.
- V LH Line, V RH Line (Center mark position of
left- hand (LH) and right-hand (RH) headlights):
Draw two vertical lines so that they intersect the
H line at each center mark (aligned with the
center of the low-beam headlight bulbs).
4. HEADLIGHT AIMING INSPECTION
- Cover or disconnect the connector of the headlight
on the opposite side to prevent light from the
headlight not being inspected from affecting
headlight aiming inspection.
NOTICE:
Do not keep the headlight covered for more than
3 minutes. The headlight lens is made of
synthetic resin, and may easily melt or be
damaged due to heat.
HINT:
When checking the aim of the high-beam, cover the
low-beam or disconnect the connector.
- Start the engine.
NOTICE:
Engine rpm must be 1,500 or more.
- With headlight leveling switch:
- Set the headlight leveling switch to 0 (zero).
- Turn on the headlight and make sure that the cutoff
line falls within the specified area, as shown in the
illustration.
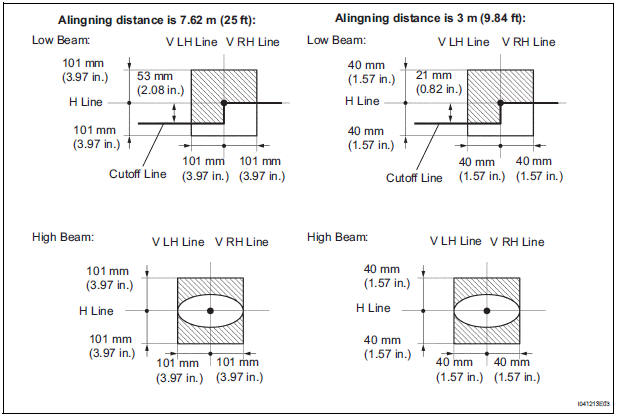
HINT:
- Since the low-beam light and the high-beam light
are a unit, if the aim on one is correct, the other
should also be correct. However, check both
beams just to make sure.
- Alignment distance is 7.62 m (25 ft):
The cutoff line is 101 mm (3.97 in.) above and
below the H line as well as left and right of the V
line with low-beam (SAE J599).
- Alignment distance is 3 m (9.84 ft):
The cutoff line is 40 mm (1.57 in.) above and
below the H line as well as left and right of the V
line with low-beam (SAE J599).
- Alignment distance is 7.62 m (25 ft):
The cutoff line is 101 mm (3.97 in.) above and
below the H line as well as left and right of the V
line with high-beam (SAE J599).
- Alignment distance is 3 m (9.84 ft):
The cutoff line is 40 mm (1.57 in.) above and
below the H line as well as left and right of the V
line with high-beam (SAE J599).
- Alignment distance is 7.62 m (25 ft):
The cutoff line is 53 mm (2.08 in.) below the H
line with low-beam.
- Alignment distance is 3 m (9.84 ft):
The cutoff line is 21 mm (0.82 in.) below the H
line with low-beam.
5. HEADLIGHT AIMING ADJUSTMENT

- Adjust the aim vertically:
Adjust the headlight aim into the specified range by
turning aiming screw A with a screwdriver.
NOTICE:
The final turn of the aiming screw should be
made in the clockwise direction. If the screw is
tightened excessively, loosen it and then
retighten it, so that the final turn of the screw is
in the clockwise direction.
HINT:
- Perform low-beam aim adjustment.
- The headlight aim moves up when turning the
aiming screw clockwise, and moves down when
turning the aiming screw counterclockwise.
1. REMOVE NO. 1 HEADLIGHT BULB (HALOGEN HEADLIGHT)
Turn in the direction indicated by the arrow and
remove the No. 1 headlight bulb.
2. REMOVE DISCHARGE HEADLIGHT BULB (DISCHARGE HE ...
1. INSTALL LIGHT CONTROL ECU (DISCHARGE HEADLIGHT)
Install a new headlight leveling motor base packing.
Install the headlight leveling motor assembly as
shown in the illustrati ...
Other materials:
Center Airbag Sensor Assembly Communication
Circuit Malfunction
DTC B1790 Center Airbag Sensor Assembly Communication
Circuit Malfunction
DESCRIPTION
The center airbag sensor assembly communication circuit consists of the
occupant classification ECU and
the center airbag sensor assembly.
DTC B1790 is recorded when a malfunction is detected in the center ...
Transmission Fluid Temperature Sensor "A"
DESCRIPTION
The ATF (Automatic Transmission Fluid) temperature sensor converts the fluid
temperature into a
resistance value which is input into the ECM.
The ECM applies a voltage to the temperature sensor through ECM terminal THO1.
The sensor resistance changes with the transmission f ...
Precaution
NOTICE:
Because the compressor operates at high voltages, wear
electric insulated gloves and pull out the service plug to
cut the high-voltage circuit before inspection.
1. DO NOT HANDLE REFRIGERANT IN AN ENCLOSED AREA OR NEAR AN OPEN FLAME
2. ALWAYS WEAR EYE PROTECTION
3. BE CAREFUL NOT T ...